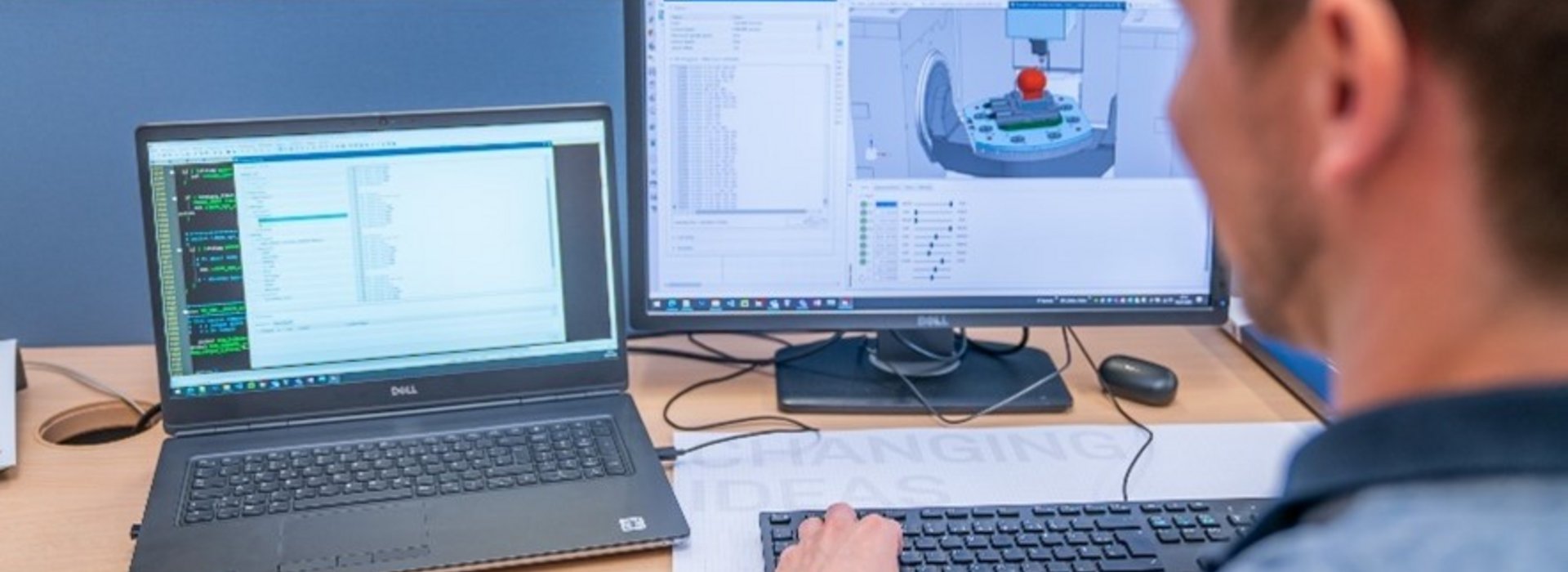
Rethinking Digital Manufacturing: Flexible NC Programming with CAM, Postprocessor, and Digital Twin
In modern manufacturing, speed, precision, and flexibility are critical. Where CNC programs once had to be manually adjusted and tested directly on the machine, a digital twin now takes over this task. The combination of powerful CAM software, a custom-developed postprocessor, and NC code-based machine simulation raises process reliability and efficiency to a new level – even before the first chip is cut.
CAM as the Heart of the Digital Process Chain
CAM (Computer Aided Manufacturing) is now far more than just a tool for toolpath planning. It forms the crucial interface between design and production. Based on 3D CAD models, complete machining strategies are created—taking into account the workpiece material, the tools used, and the clamping devices. However, it’s only with a postprocessor precisely tailored to the machine that the CAM system reaches its full potential.
Postprocessor Development – The Bridge to the Real Machine
The postprocessor translates neutral CAM data into the specific NC code required by the individual machine. But it’s about much more than syntax—it holds the true "intelligence" of the machine. Machine cycles, axis control, zero-point management, and tool calls all need to be perfectly matched. Especially in single-part and small-batch manufacturing with high part variety, a customized postprocessor makes all the difference. It enables even complex strategies to be executed repeatably and reliably—automated and process-secure.
NC Code-Based Machine Simulation – The Digital Twin in Action
Maximum efficiency is achieved when the generated NC code is verified in a realistic environment before actual machining begins. This is where the digital twin comes into play: a simulation environment that mirrors not just the machine’s kinematics and working area, but also real clamping devices and 3D tools. Unlike simple CAM simulations, this simulation is based on the actual NC code—that is, precisely what the machine will later execute.
The result: collision-free processes, optimized movements, and a dramatic reduction in setup and trial times.
Flexibility in Manufacturing – Offline but 100% Process-Secure
For frequently changing parts or complex clamping concepts—such as multi-part setups—this kind of flexible NC programming pays off. Thanks to precise 3D models of clamping devices and tools, programs can be created completely offline, including realistic simulation. Programming no longer ties up the machine, and even complex re-clamping or multi-axis scenarios become manageable.
Another key advantage:
Simulation also uncovers optimization potential, such as unnecessary tool changes, suboptimal feed rates, or excessive air cuts between and within operations. The result is not just greater safety, but significantly higher productivity and cost-efficiency.
Conclusion
Digital manufacturing thrives on connected, precise, and intelligent systems.
Those who combine CAM, postprocessor, and digital simulation in a targeted way create a production environment that not only meets current demands but actively uncovers optimization potential—with maximum flexibility, process reliability, and speed. The digital twin makes it possible.
TCM has evolved accordingly, creating in-house capabilities to combine its long-standing tooling expertise with modern CAM programming and machining simulation.
The result benefits our customers directly:
Efficient and process-reliable part production, along with fast project execution, are guaranteed with this methodology—leading to real competitive advantages in the market.
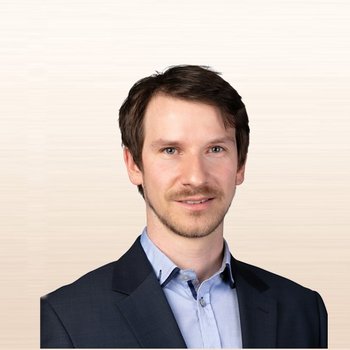
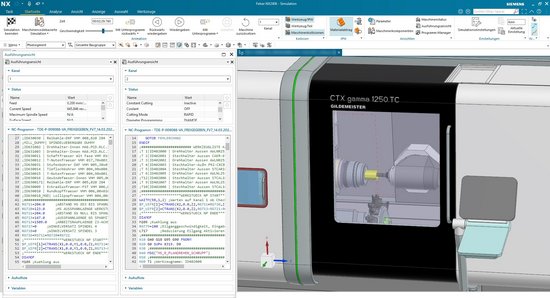
CAM-based simulation of multitasking machines
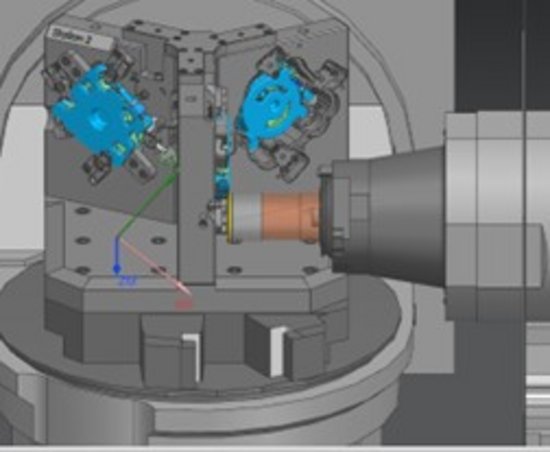
Simulation of machining and collision detection
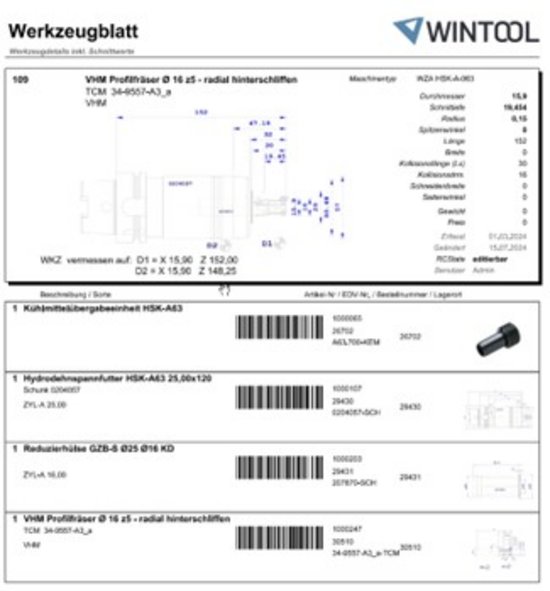