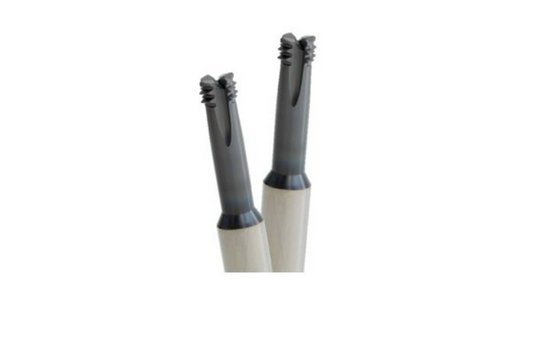
SHORTER SET-UP TIMES - LONGER LIFE
In the in-house machining laboratory, a newly developed solid carbide thread milling cutter from OSG was tested, with which threads can be milled by means of spiral interpolation into the full material.
Thus, no previous drilling for the production of threaded core holes is necessary.
These attempts were inspired by TCM customers who constantly process difficult-to-machine materials (such as Hastelloy, Vanadis).
Due to the high toughness of these materials, tool breaks occur repeatedly to taps during the tapping process
The production of rejects on workpieces made of these expensive materials is therefore often the result.
Due to the clamping properties of these materials and due to the high wear on the taps, in some cases non-true threads are produced.
When thread milling in the full, only short shavings are produced that can be easily removed with the internal cooling mechanism of the tool. Furthermore, the diameter of the thread can be easily corrected with the aid of the CNC control, so that the lateral impact forces can be well compensated.
Results and findings from the test series: (download information)
• Perfect trueness
• High surface quality and profile fidelity of thread flanks
• Thread absolutely burr-free
• No conicity of the thread
• Finished thread with only one milling cycle, no blank cut required
• Tool was tested in four materials (no wear can be measured after 50 threads)
• High process stability
The newly developed thread milling cutter was convincing in all four tested materials and is therefore recommended for the production of internal threads for chrome nickel steels, as well as for titanium and superalloys.