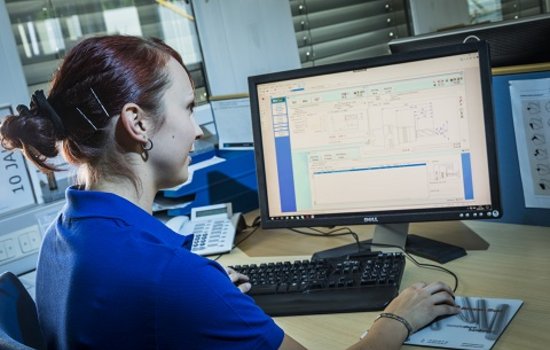
The power is in the cutting edge! - Part 2
Decisive productivity increases can be achieved through the use of special tools! At TCM, they are being continuously designed and individually tailored to the respective processing case. Particularly, the tolerances and material properties of the component must be observed.
An optimal design of the chip spaces and the precise guidance and arrangement of the internal cooling channels of the tool are crucial here! Since larger quantities of chips are created if several cutting edges are used at the same time, these have to be removed from the processing point as quickly as possible.
Challenging materials
High cutting speeds and innovative machining strategies frequently cannot always be achieved due to the material and component properties.
Often the only way to get faster is to increase the feed values!
With cutting tools, the feed / cutting edge must not exceed or fall below a certain value. The desired, higher machining feed rate and thus time savings, can only be achieved by significantly increasing the number of teeth.
Increasing the feed rate in the machining process has a far greater impact on the machining time than increasing the speed (cutting speed)!
The increased number of teeth on the tool (narrow tooth pitch) results in smaller chip spaces in front of the cutting edge. When developing these tools - for the design and direction of the cooling channels to the individual cutting edges - it is necessary to break new ground.
Our team at TCM is committed to mastering these innovative paths, on behalf of your productivity!