
Reconditioning of gear cutters and broaching tools at TCM Polska in Polkowice:
Since the foundation of TCM (1986), solid carbide shank tools of all kinds have been continuously reground and reconditioned. After focusing our grinding competences in the service center in Polkowice, TCM Polska has again invested heavily in machine and measuring equipment in order to be able to regrind and measure hobs and broaches in the highest quality. Especially in TCM tool management projects, where gears and gear components are produced and customers broach internal profiles and connectors in large quantities, the frequent reconditioning of these valuable tools is of utmost importance. Furthermore, hobs and broaches usually have very long procurement times.
Regrinding of hobs and pinion gears:
In our grinding store, HSS-E, HSS-PM, as well as solid carbide hobs are reground in AAA quality. The rounding of the profile cutting edges as well as the recoating is done at the coater Oerlikon Balzers, which operates its coating facilities at the same location. As a result, lead times of only 2 -3 weeks can be realized. In the event of emergencies following tool breakage or machine faults, it is often necessary to react even faster. The final inspection of the gear cutters is carried out by means of Zoller Hob-Check and Werth measuring machines, which enable us to measure tooth pitch and tooth profile accurately. Measurement reports can also be provided to our customers for each regrind. In addition, TCM maintains an accompanying run card for each gear cutting tool. This chart shows the amount of grinding, the number of regrinds and the tool life achieved in the process. Under optimum conditions (tooth flank wear not exceeding 0.15 mm), hobs can be reground 14 - 18 times. The size of the cutting edge rounding, as well as the type and thickness of the coating, is precisely coordinated with Oerlikon for the customer's particular application. When the minimum tooth thickness is reached, which is precisely defined for each gear cutter, the tools can then undergo another machining process before they are disposed of. The customer is informed in good time so that new tools can be replanned.
Cutter wheels for gear shaping and solid carbide cutters for hobbing (power skiving) can also be reground at TCM. These tools are ground exclusively on the face of the rake face. Here, it is important to achieve as smooth a surface as possible in order to obtain perfect cutting edges and to avoid built-up edges.
Generally, we use modern diamond grinding wheels, often combined with additively manufactured grinding nozzles and carefully filtered high-performance cutting oil. Optimized cooling at the grinding point is important so that the cutting material is affected as little as possible thermally.
Regrinding of round broaches and broach segments:
Before grinding, each broach is subjected to a precise visual inspection. In this process, the maximum flank wear of the milling cutters is determined, according to which the maximum amount of grinding is defined.
Round broaches are reground exclusively on the rake face. Due to the many rows of teeth with increasing diameters on circular broaches, the tooth pitch and the respective diameters in the CNC grinding program must match the pitch of the tool exactly. After grinding the rake face with the rake angle specified by the manufacturer, the grinding burr must be completely removed from all broach teeth. In an additional visual inspection, a final check is made to ensure that all wear marks on the profile teeth have also been completely ground away. The round broaches are not recoated after regrinding. However, the original coating of the new tool is still present on the free surfaces of the cutting edges.
Broaching segments for the production of toothing of racks, usually consist of 4 broaching segments which are mounted one behind the other in a slide holder. The gearing is produced in only one vertical stroke at high speed. Segments 1 and 2 do the preliminary work, while segments 3 and 4 broach the tooth profile deeper from tooth row to tooth row until the last tooth rows on segment 4 take over the calibration of the final profile. This method is used to produce racks for steering gears in large quantities.
When reconditioning the broach segments, there are basically 3 regeneration stages. Starting with the grinding of the rake faces alone, continuing with the grinding of the rake and flank faces, and ending with the complete reprofiling of the tooth profile (resetting of the entire tooth profile including relief grinding). With the new "Schneeberger Corvus" grinding machine, all 3 regeneration stages can now be carried out in-house at our company, which drastically reduces the throughput times when reconditioning the broach segments.
The regrinding and reprofiling of rolled bars for the large-scale production of shafts with keyways, splines, threads and profile grooves is the next task we will face. This will complete the TCM regrinding portfolio by the end of 2021.
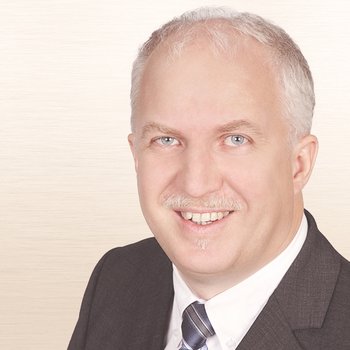
With more than 40 years of broad cutting experience, TCM is an attractive technology partner.
oscheibenbauer@tcm-international.com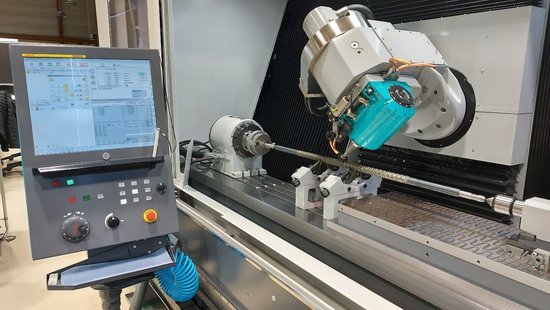
Grinding round broach
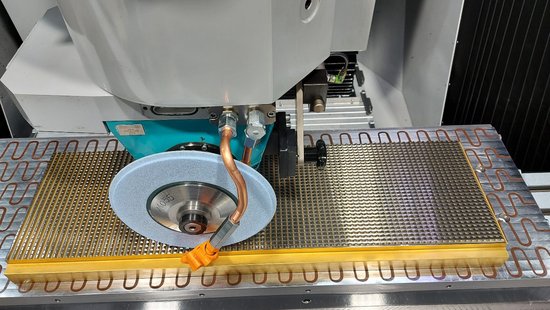
Reprofiling of a broach segment
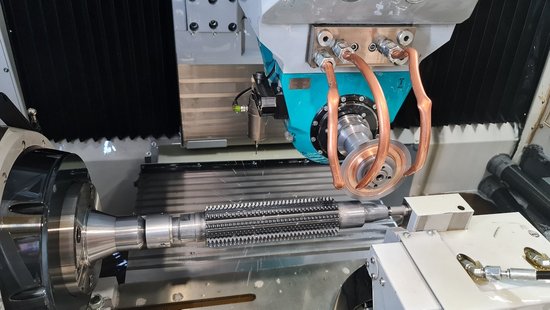
Grinding of a hobbing cutter
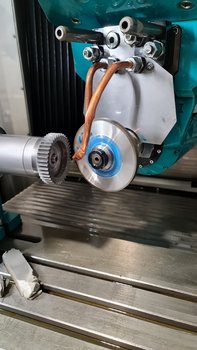
Grinding a shock wheel
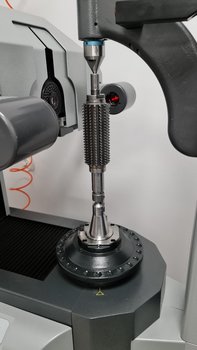
Zoller Hob - Check
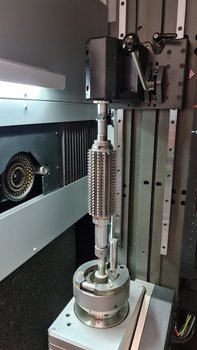