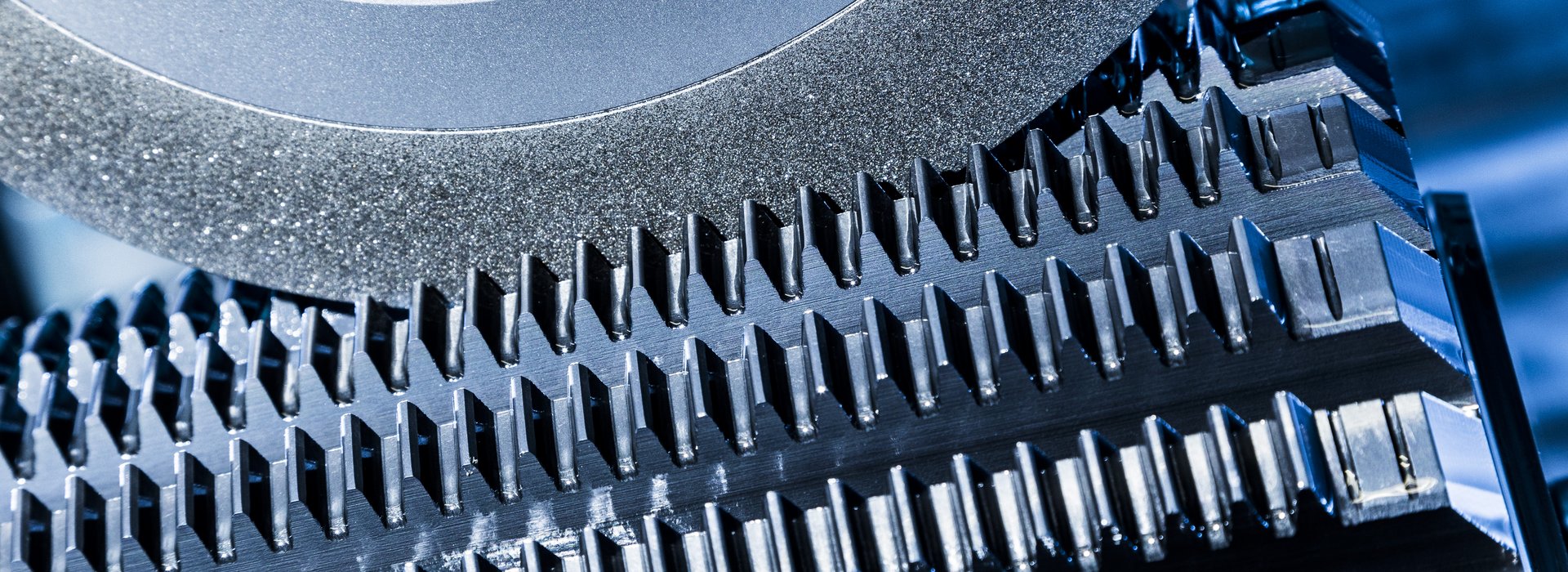
Optimization of grinding processes using additively manufactured components!
In addition to the permanent optimization of machining processes with defined cutting edges, TCM also has tool experts with special expertise in the optimization of grinding processes in the team.
The task of these grinding specialists is to continuously improve grinding processes and to ensure that the grinding technology at TCM is always up to date.
This applies to both the grinding processes in cylindrical grinding in large-scale production at our customers' premises, as well as the grinding processes in tool grinding in the TCM tool grinding shops
The grinding processes in our customers’ buildings are mostly delivered and adjusted by the grinding machine supplier together with the grinding wheel manufacturer. In most cases, the customer does not have the detailed grinding knowledge on site which means that these processes, as soon as the desired component quality has been achieved, often remain unchanged for many years.
Since grinding processes are usually one of the top costs of a production line, the optimization of the grinding processes has always been an important topic for TCM.
A drop in the tool life (increased dressing cycle) also has a direct effect on the significant increase in tool costs per part.
Due to the high costs of the CBN and diamond wheels and the high average delivery time of 10-12 weeks, the grinding processes are constantly monitored and looked after in the TCM tool management on site.
Today, almost without exception, CBN-coated grinding wheels with steel bodies are used as grinding media for hardened steel parts in large-scale production.
When grinding and sharpening carbide tools, diamond grinding disks are used.
The grinding wheels for both applications have already been developed to a great extent by the various manufacturers, which means that only minor improvements have resulted in grinding wheel tests with newly developed grinding substrates, binder materials or new suppliers on the market (which are still being carried out continuously).
The periphery around the grinding wheel offers significantly more optimization options.
Due to today's extremely high grinding speeds on the grinding wheel circumference, more attention must be paid to the cooling of the grinding point (grinding gap) than was usual in the past.
Insufficient cooling of the grinding point quickly leads to grinding burn when grinding tempered steel parts and thus to an inadmissible softening of the hardened steel. When grinding tools made of tool steel or powder metallurgical steel, similar effects occur
Especially when grinding carbide cutting edges, if the grinding is too fast or the infeed is too high, extreme heat input on the tool cutting edge occurs. This heat input permanently damages the carbide matrix and leads to thermal cracks.
The consequence is premature failure of the cutting edges
When optimizing a grinding process, a precise ACTUAL analysis is essential, which is carried out by our grinding expert at the customer's,
The following data and parameters are determined:
• State of the currently used grinding machine
• Check of the currently used grinding wheel ( Manufacturer, abrasive coating)
• Check of the currently used cutting data ( vc in m/s and grinding feed)
• Current dressing cycle and dressing tool status
• Cooling of the grinding wheel (CM pressure, filtering, coolant jet positioning)
• Determination of the current grinding time / part or / tool
• Determination of the current grinding costs / component (CPU) if required
• The optimization goal is discussed and agreed with the customer
As mentioned before, faster grinding and thus more productivity can be achieved primarily through improved cooling. In most of the cases that we have observed with customers, the coolant sprays either through flexible coolant hoses with flat nozzles or through flexible copper pipes to the grinding point.
At best, this arrangement cools the grinding wheel, but not the grinding point where the actual material is removed. In addition, the air cushion that permanently surrounds the rapidly rotating grinding wheel prevents the coolant from reaching the grinding gap at all
Thanks to the new possibilities of additive manufacturing, we can now additively manufacture coolant nozzles for grinding operations in which the individual cooling channels can be optimally adapted to the workpiece contour to be ground.
In addition, this production method can be built very slim so that the coolant nozzles can be moved much closer to the grinding point.
Due to the improved arrangement and positioning of the coolant nozzles, the grinding times in the tests carried out by TCM could be reduced by between 20 - 30%!
(with the same dressing cycle and component quality)
Even when grinding tools in our grinding shops, the better cooling leads to a faster throughput of the tools, which significantly reduces the delivery time for our customers when reconditioning the often expensive tools.
Furthermore, the better cooling during tool grinding means that the cutting material is protected, which again results in consistently long service lives in use.
The application of this technology is particularly advantageous when grinding larger tools with higher removal volumes and with increased tooth wear, as can often occur with gear cutting tools or broaches.
Do you have grinding processes with high costs or long grinding times?
Put us to the test!
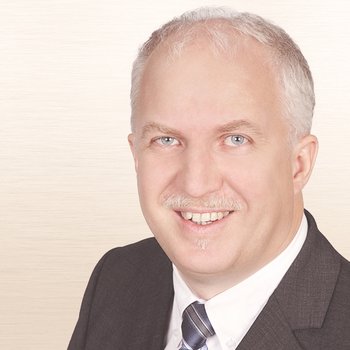
With more than 40 years of broad cutting experience, TCM is an attractive technology partner.
oscheibenbauer@tcm-international.com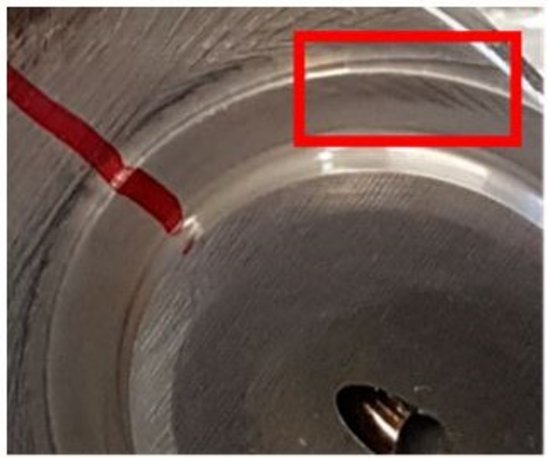
Grinding burn crankshaft bearings
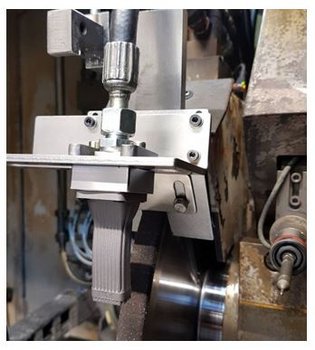
Additive coolant nozzle for cylindrical grinding of crankshaft main and pin bearings Concept and execution
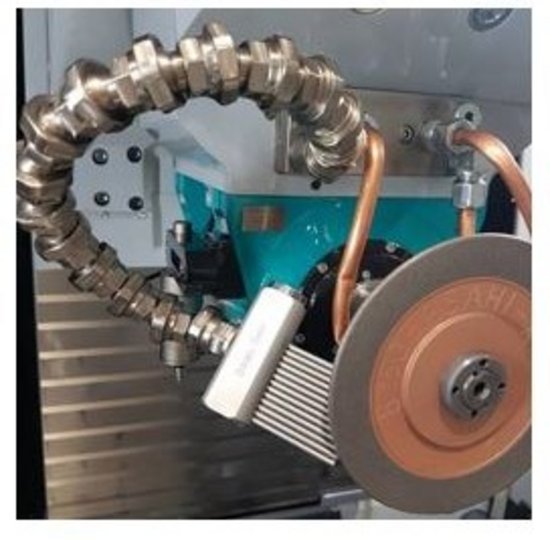