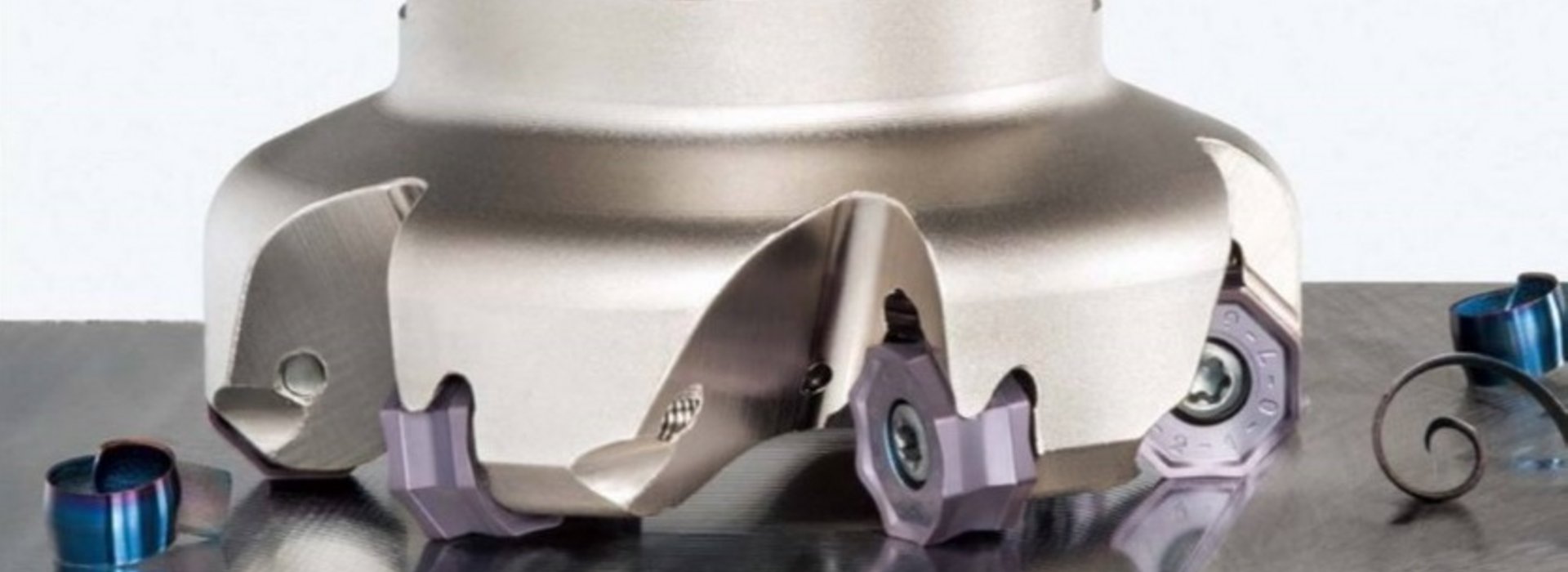
Modern face milling and cutting cost consideration:
In the field of milling metallic components, face milling still accounts for a large share of the total machining time. The high number of inserts used in face milling cutters, combined with difficult conditions for rough milling of cast and forged skin, often result in considerable tool costs. There is also a large savings potential in the optimal matching of the insert size used to the maximum required cutting depth on the component.
In the course of several TCM tool management analyses carried out at various production companies, we have frequently encountered the following critical points in the area of face milling:
1) Outdated milling systems in use with too few cutting edges / insert
2) Inserts corner milling cutters are mostly used for face milling as well
3) Inserts with high cutting edge length are used with too low depth of cut
4) Vibrations during face milling of thin-walled components
5) Unsuitable cutting values, especially too low feed/tooth fz
1) Outdated milling systems in use with too few cutting edges / insert:
A few years ago, face milling cutters with 4-cutting inserts with positive cutting geometry (SEKN, SEKR, SEHW) were the measure of all things. Subsequently, due to new possibilities in sintering technology, face milling systems with double-sided inserts with up to 8 cutting edges / insert have become established on the market.
In the meantime, this technology has also been extended to double-sided inserts with 5 angular inserts (PENTA 10 cutting edges / insert) , as well as with 6 angular inserts (HEXA, 12 cutting edges / insert).
The latest development is face milling cutters with 8 square inserts (OKTO, 16 cutting edges/insert) and an angle of attack of 45°, which ensures optimum distribution of the cutting forces in both axial and radial directions during face milling.
Due to the octagonal shape of the insert, the maximum cutting depth is usually limited to 4 - 5 mm. However, the insert seats are then manufactured in such a way that square inserts (with 8 cutting edges) for higher cutting depths can also be installed and used in the same cutter.
The side faces (flanks) of the inserts are inclined inward on both sides. This dovetail design results in perfect positioning and an even better hold of the insert in the cutter body. Due to the strong positive rake angle which is sintered into the inserts with the chip groove, a soft cut and good chip formation results despite the negative positioning of the insert in the cutter.
2) Inserts corner milling cutters are mostly used for face milling as well:
Often, for reasons of convenience, the inserts - corner milling cutters available in the machine are also used for milling any flat surfaces.
However, this results in a few significant disadvantages for WSP corner milling cutters compared to 45° face milling cutters:
- The 90° angle of attack of the corner milling cutter results in 100% radial cutting force, which causes
an extreme load on the spindle radial bearings.
- Vibration tendency with longer overhangs
- Inserts for corner milling cutters usually have significantly fewer cutting edges / insert
- Less feed / tooth possible than with face milling cutter, with the same cutting depth
- Poorer surface finish due to much smaller face cutting edges
Recommendation TCM:
Only use corner milling cutters for face milling if a 90° shoulder actually has to be produced on the component at the edge of the milled face!
3) Inserts with high cutting edge length are used with too low depth of cut:
For both insert corner and face milling cutters, the same type of cutter is available with different insert sizes. Many customers try to reduce the variety of inserts and buy only the larger insert size of the system. The problem is that finishing cuts, cuts with small stock allowances, or cuts on unstable components are then machined with inserts that are definitely too large. As a result, 70 - 80 % of the possible cutting edge length is not used! TCM recommends optimally matching the insert sizes to the cutting depths to be mastered and, if necessary, buying a few more cutter bodies.
4) Vibrations during face milling of thin-walled components:
For face milling of thin-walled components (gray cast iron or aluminum housings, steel welded constructions, etc.) or high-alloy stainless steels, we recommend face milling cutters with highly positive cutting geometries in order to keep the cutting forces as low as possible to effectively counteract any vibrations. Problems may arise here when using milling inserts that can be used on both sides!
Currently, the most economical solution for such applications is face milling cutters with single-sided 8-flute inserts with a strongly positive rake angle and large clearance angle.
5) Unsuitable cutting values, especially too low feed/tooth fz:
For good tool life and high productivity, the tooth feed for face milling should be selected as high as possible. Due to the slight rounding of the cutting edges of commercially available milling inserts, the feed / tooth fz should never fall below the value of 0.1 mm!!!
Usual fz values for conventional face milling are:
fz = 0.2 - 0.3 mm, or 0.4 - 0.8 mm for large machines.
Finally, a comparison of cost / cutting edge between standard insert face millers and the above face mill models, using commercial net prices:
cutting single sided / price / price /
per insert double sided insert cutting edge
Corner milling cutter
insert high positive type A 2 single sided 11,50 € 5,75 €
Milling insert SEKR 4 single sided 7,95 € 1,99 €
Milling insert SNGU 8 double sided 13,90 € 1,74 €
Milling insert OWHU 8 single sided 13,57 € 1,70 €
Milling insert PNCU 10 double sided 13,45 € 1,35 €
Milling insert HNGJ 12 double sided 13,80 € 1,15 €
Milling insert ONMU 16 double sided 14,83 € 0,93 €
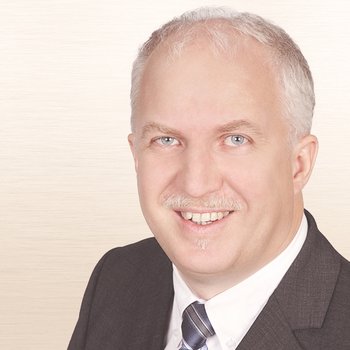
With more than 40 years of broad cutting experience, TCM is an attractive technology partner.
oscheibenbauer@tcm-international.com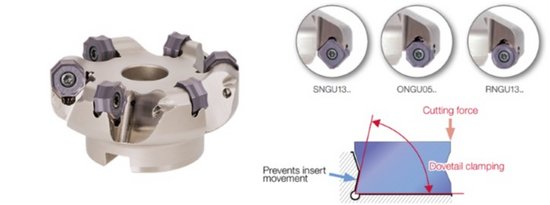
to 1: Modern face milling cutter for the use of 3 plate types in the same cutter base body.
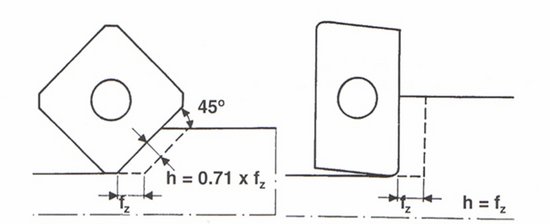
to 2: Difference between chip thickness plan and corner milling cutter with the same tooth feed fz
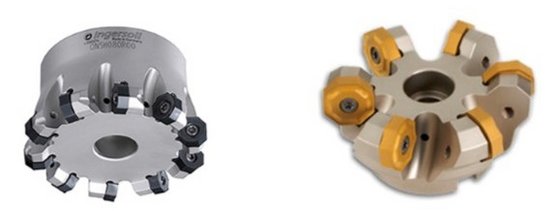
to 3: Modern face milling cutter with 2 different plate sizes
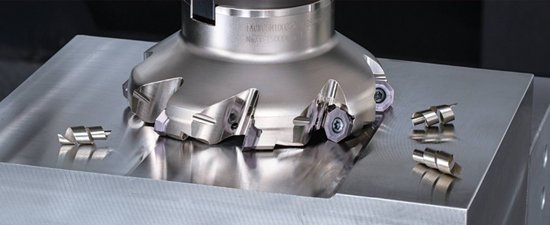