Changing Ideas
with BMW Group
A story of success
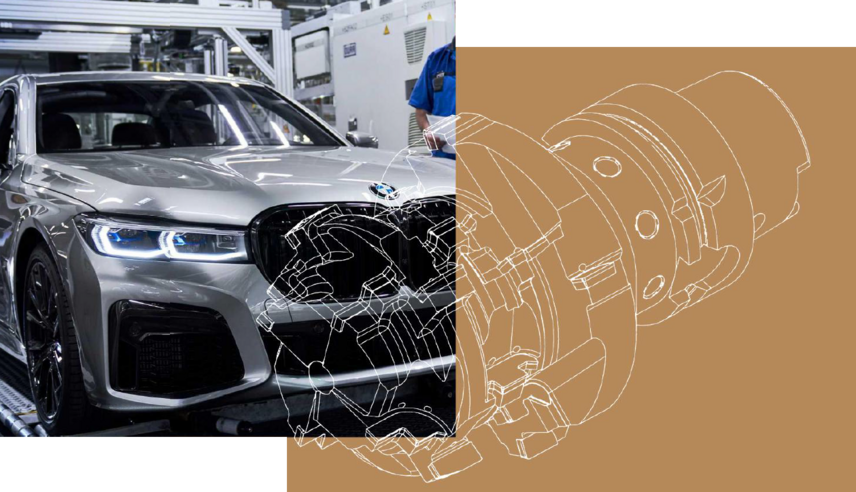
An der Spitze zu bleiben erfordert heutzutage ein Tool Management, das nicht nur präzise ist, sondern das "absolut präzise" ist. Und ein Tool Management, das am besten auch noch die Werkzeugkosten um 50% reduziert.
Aufgabenstellung
Das BMW-Werk Landshut hat den Anspruch, dem Wettbewerb immer eine Idee voraus zu sein. Das betrifft auch den Umgang mit Werkzeugversorgung und Werkzeugvoreinstellung.
Lösung
Das Tool Management von TCM (Level 6) bringt neben einer fehlerlosen Werkzeugversorgung auch noch garantierte Produktivitätssteigerungen. Dafür wird der gesamte Produktionsprozess laufend analysiert und optimiert. Ergebnis: Die Werkzeugkosten wurden halbiert.
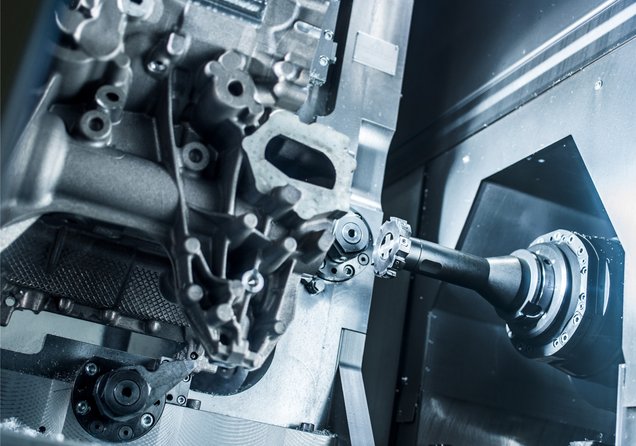
Unser Kunde: Das BMW Group-Werk in Landshut
Im BMW Group Werk Landshut sorgen rund 3.600 Mitarbeiterinnen und Mitarbeiter Tag für Tag dafür, dass in jedem BMW, MINI und Rolls-Royce ein Stück Landshuter Innovationskraft steckt.
Als Kompetenzzentrum für Leichtbau und Elektromobilität entstehen so Trends für eine gesamte Branche.
Die Herausforderung
TCM International hatte die Aufgabe übernommen das BMW Group-Werk in Landshut bei der Werkzeugversorgung und Werkzeugvoreinstellung zu unterstützen.
Der Anspruch von TCM International? Eine neue Perspektive für die Arbeit im Shopfloor zu erarbeiten.
Wie alles begann
Mit der TCM Tool Analyse wurden die gewohnten Abläufe,
mögliche Verbesserungspotenziale und auch die Qualität der Stammdaten erhoben. Der unvoreingenommene, objektive Blick von außen ist unbestechlich und zeigt Wege, wie die Prozessqualität gesteigert werden kann. Dabei werden neben dem Status quo auch die Verbesserungsmöglichkeiten in den Bereichen Einkauf, Organisation und Werkzeugtechnologie erarbeitet. Im gegenständlichen Fall ermöglichte das Ergebnis der Analyse einerseits eine unmittelbare, aber auch ein stetige Produktivitätssteigerung im Werkzeug-Management.
Der Beitrag von TCM: Tool Management Level 6
Als Weiterentwicklung des hocherprobten TCM Tool Management entwickelten die Spezialisten von TCM International ein neues „Level 6" für mehr Effizienz und deutliche Produktivitätssteigerungen.
Level 6 beinhaltet zusätzlich zur klassischen Werkzeugkostenbetrachtung auch innovative Bearbeitungskonzepte, die in das jeweilige Geschäftsmodell integriert werden. Somit kann TCM einerseits den Vorteil der reduzierten Werkzeugkosten und darüber hinaus auch noch ein vorab definiertes Maß an Produktivitätssteigerung während der Vertragslaufzeit bieten.
Ein entscheidender Aspekt dabei ist, dass das Ausmaß der höheren Produktivität um ein Mehrfaches größer ist, als die Einsparung der Werkzeugkosten. Durch die Integration in das von TCM entwickelte SAP Tool Management COCKPIT können künftig zusätzlich Prozesse effizient gesteuert und optimiert werden. Die Leistung von TCM ermöglicht es seinen Kunden, wie z.B. der BMW Group, von langfristigen und nachhaltigen Optimierungen zu profitieren, die eigene Wettbewerbsfähigkeit zu verbessern sowie jährliche Einsparungen zu verzeichnen. Ebenso damit verbunden war die Einführung von Wintool und die Instandsetzung und Wiederaufbereitung der PKD-Werkzeuge.
Das Ergebnis
- Werkzeugkosten halbiert
- Laufende Beratung in der Auslegung neuer Projekte
Max Lankes über
Übermorgen ist heute
schon vorgestern
Seit fünf Jahren unterstützen die Tool Manager von TCM International die BMW Group im Werk in Landshut. Wir haben TCM Tool Manager Max Lankes um eine Bilanz gebeten. Hier berichtet er, was man gemeinsam gelernt hat, warum man ruhig persönlich werden sollte, und was die Stückzahl 1 mit der Zukunft zu tun hat.
Die Fakten sind schnell erzählt: Im BMW Group-Werk Landshut sorgen 3.600 MitarbeiterInnen Tag für Tag dafür, dass in jedem BMW, Mini und Rolls Royce ein Stück Landshuter Innovationskraft steckt. In diesem Kompetenzzentrum für Leichtbau und Elektromobiltät startete vor fast fünf Jahren TCM International, der Tool Management-Spezialist mit österreichischen Wurzeln, ein sogenanntes „Level 6“-Projekt.
„Level 6“ klingt gut – aber was genau ist das?
Das Tool Management-Level 6 beinhaltet über die klassische Werkzeugkostenbetrachtung hinaus auch innovative Bearbeitungskonzepte, die in das jeweilige Geschäftsmodell integriert werden. Ein entscheidender Aspekt dabei ist, dass das Ausmaß der höheren Produktivität um ein Mehrfaches größer ist, als die Einsparung der reinen Werkzeugkosten.
Im Fußball misst man Erfolg in Toren – wie lässt sich der Erfolg eines Tool Management-Projekts messen?
Max Lankes: In der Fußballersprache ist uns, denke ich, ein Kantersieg gelungen! Die entscheidenden Tore? Wir haben über die Jahre ein Minus von 50 Prozent bei den Werkzeugkostenerreicht – eine vorbildliche Leistung aller Beteiligten. Durch einen stabilen und gleichzeitig flexiblen Versorgungsprozess gibt es faktisch keine Maschinen-Stillstände mehr und dadurch viel mehr Ruhe in der Produktion. Und was mich persönlich am meisten fasziniert: Es wurde gemeinsam mit BMW Group-Mitarbeitern weit über die eigentliche Kernaufgabe Zerspanung hinaus gedacht und gearbeitet und damit in vielerlei Hinsicht Neues und Aufregendes in den Produktionsprozess gebracht.
Was braucht es dazu?
Neben einer gehörigen Portion „high tech“ von Kundenseite, also vom BMW Group-Werk Landshut, und von unserer Seite als Dienstleister, braucht es vor allem eine noch größere Portion „high touch“. Um es konkret zu sagen: Der wichtigste Erfolgsfaktor ist, wie sich die Menschen im Team verstehen, nicht nur fachlich, sondern auch persönlich. In unserem Fall haben zum Beispiel die beiden Technologen aufseiten BMW Group und TCM nicht nur im Thema Werkzeug einen phantastischen Job gemacht, sondern haben sich auch Schnittstellen angeschaut und sind tief in den gesamten Produktionsprozess eingestiegen. Konkret meint das, dass die vor- und nachgeschalteten Prozesse wie Vorbearbeitung, Messen, Waschen und vieles mehr miteinbezogen wurden und so ein toller Effekt auf das Produktionsergebnis erzielt werden konnte.
Was hat TCM von der BMW Group gelernt? Und was die BMW Group von euch?
Ein wichtiger Punkt war sicher, wie klug man dort mit Innovation umgeht – nämlich neugierig genug auf dem Weg in die Zukunft, aber nicht Hals über Kopf. Und umgekehrt? Wir haben sicher überrascht, wie schnell und unkompliziert wir plötzlich auftauchende Probleme lösen können. Beim „firefighting“ sind wir richtig gut. Und ja – ich denke, dass unsere Hersteller-Unabhängigkeit schon ein wertvoller Beitrag ist. Man kann von uns lernen, dass das richtige Werkzeug zur richtigen Zeit am richtigen Ort sein muss – aber welcher Name draufsteht, ist für uns und für die Effizienz des Prozesses nicht entscheidend.
Apropos Zukunft – was kommt aus Ihrer Sicht auf die zerspanende Industrie zu?
Ehrlich gesagt glaube ich, dass es uns momentan so ähnlich geht wie Columbus auf seiner großen Reise. Wir wissen ungefähr, wo sich dieser „Kontinent Digitalisierung“ befindet. Und ja, wir finden immer wieder spannende neue Inseln. Aber wir finden uns auf der Fahrt in die Zukunft auch noch oftmals im Nebel wieder. Das kann man jetzt als Risiko sehen, oder als Chance.
Wir bei TCM sehen es als Chance, für uns und für die Branche. Unser Motto heißt „Changing Ideas“, also kurz gesagt: Wir wollen Perspektiven verändern. Lassen sie mich ein Beispiel nennen: Wenn in absehbarer Zeit ein C02-Grenzsteuersatz eingeführt wird, dann wird die Perspektive „wie sparen wir weitere Sekunden im Prozess“ nicht mehr reichen. Dann werden wir sie um „wie ressourcenschonend sind unsere Prozesse“ erweitern müssen. Eine spannende Herausforderung.
Was hat TCM zum Thema Zukunft im Köcher?
Uns ist klar, dass übermorgen heute schon vorgestern ist. Darum müssen wir unbedingt heute schon die zunehmende Komplexität in der Fertigung beherrschen lernen. Wir sehen uns und die Branche zusehends mit höherer Bauteilkomplexität und kleineren Losgrößen konfrontiert – Stichwort „Stückzahl 1“. Daraufhin haben wir uns in den letzten Jahren gezielt eingestellt und unsere eigenen Softwarebausteine danach ausgerichtet. Das beginnt bei den Stammdaten (Tooltracer.com), geht über den kompletten Rüstprozess (WinTool.com) und endet bei der systemgestützten Bereitstellung von Werkzeugen (Toolbase.de). Sie sehen, wir haben unseren Tool Management-Kreislauf kontinuierlich weiterentwickelt. Anders könnten wir Projekte mit beispielhaft mehr als 5.000 verschiedenen Werkzeugen nicht effizient managen. Im Herbst starten die nächsten Kundenworkshops, bei denen wir gemeinsam mit unseren Kunden weitere Optimierungsschritte festlegen. Für uns kann übermorgen kommen!